Innovative chemical reactors are being developed for various processes, seeking more effective systems, within the trend towards intensification of processes to achieve more compact, safer equipment with less environmental impact. Work has been carried out on two types of innovative reactors: membrane reactors and two-zone fluidised bed reactors.
In membrane reactors, a catalyst bed is combined with a membrane that removes one of the reaction products. In this way, the production is increased or it is possible to operate under milder conditions. This is particularly interesting for reactions where the equilibrium conversion is limited by thermodynamic equilibrium. In other processes, one of the reactants is distributed along the catalyst bed using a porous membrane. This is appropriate when maintaining a low concentration of that reactant allows for improved selectivity, as has been observed in several catalytic oxidation processes.
In two-zone fluidised bed reactors, two zones with different reaction atmospheres are created in a catalytic fluidised bed reactor by feeding two different streams (e.g. an oxidising and a reducing stream) at two different points in the bed. In this way, two different reactions can be carried out in the same reactor, e.g. catalytic reforming in one area and catalyst regeneration in another. This may be applicable in processes where catalyst deactivation makes the use of conventional reactors inadvisable.
Most of the current research is focused on the development of improved reactors for the production of liquid e-fuels, i.e. methanol and dimethyl ether. Those can be produced from CO2 and hydrogen obtained with renewable sources (solar o wind), and thus contribute to reduce the dependence of our society on fossil fuels.
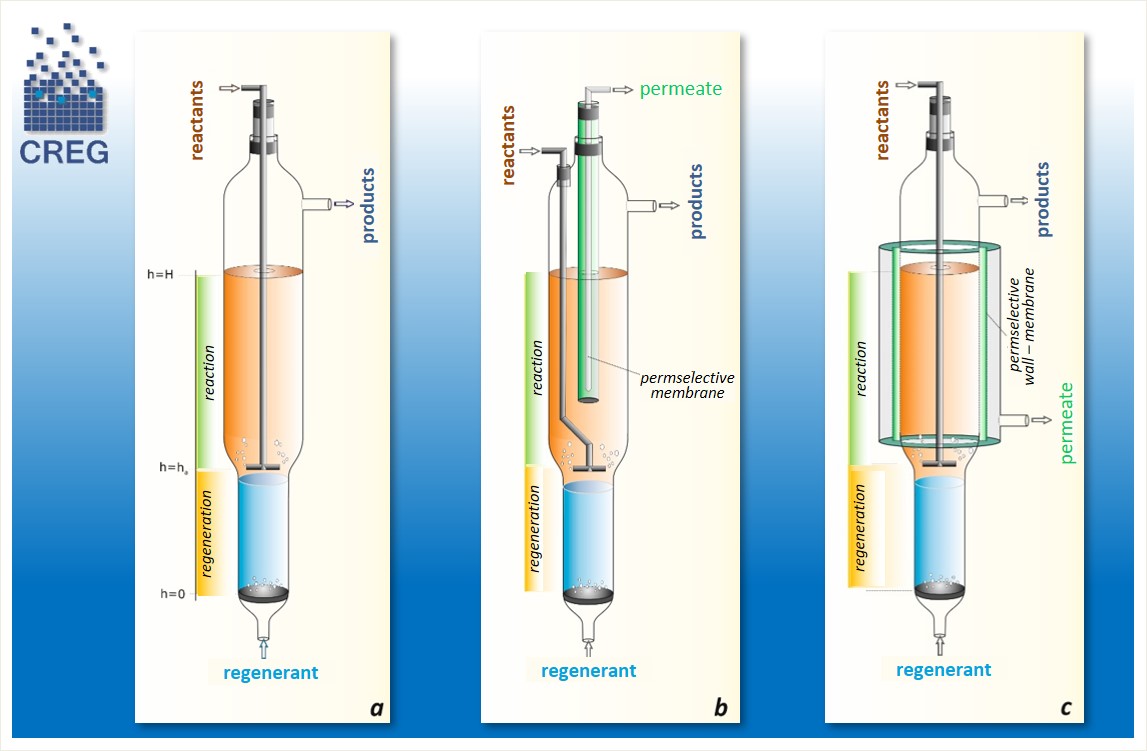